Las técnicas de Lean Manufacturing lograron transformar el mundo de la industria durante los años 2000.
Inventado en Japón, donde no hay ni recursos naturales ni exceso de espacio para la producción, la fabricación tenía que ser ‘esbelta’, y eficiente para proporcionar valor.
A su vez, el éxito de la industria japonesa resultó en una explosión de interés en todo el mundo. El Sistema de Producción Toyota es considerado en gran medida como el precursor de la filosofía Lean Manufacturing.
El Lean Manufacturing realmente pone de cabeza algunos de los conceptos que venían siendo utilizados en la industria tradicional. Pero más que un método definido de mejora de procesos, es un método de transformación organizacional.
El Lean Manufacturing se puede desglosar en cinco principios fundamentales:
- Valor
- La cadena de valor
- Flujos
- Procesos ‘Pull’
- Mejora continua
Lean Manufacturing: Valor
En primer lugar, el Lean Manufacturing reduce los procesos productivos a lo básico.
Hay una variable crítica que define todo negocio: el valor. El valor se define como la cantidad que alguien está dispuesto a pagar por algo, y es esto, y sólo esto, lo que permite que cualquier negocio funcione.
Más específicamente, cuando una persona u organización desea un producto o servicio por el que está dispuesta a pagar, se crea valor. Es este deseo de intercambiar recursos monetarios con un producto o servicio que crea valor.
Por lo tanto, definir este valor es el primer paso en la fabricación ajustada o ‘esbelta’. El pensamiento esbelto debe comenzar con un intento consciente de definir con precisión el valor en términos de productos específicos con capacidades específicas ofrecidos a precios específicos a través de un diálogo con clientes específicos.
Al definir este valor, el fabricante lean debe definir:
- ¿Qué producto satisfará la necesidad del cliente?
- ¿Qué características tendrá?
- ¿Qué nivel de calidad debe tener?
- ¿Qué precio pagará?
- ¿Cómo utilizarán el producto?
- ¿Qué requisitos de mantenimiento tiene?
- Cualquier otro artículo que forme parte de la definición de valor por parte del cliente.
Por ejemplo, la propuesta de valor para una empresa de fabricación de muebles es vender muebles a un precio justo, sin defectos que duren 10 años bajo un uso intenso.
Lean Manufacturing: La cadena de valor
Una vez definido el valor desde la perspectiva del cliente, se identifican los pasos necesarios para crear ese valor. Cada paso importante del proceso se detalla y se grafican. Normalmente hay múltiples líneas de producción paralelas que convergen en un solo punto de la fabrica (como el envasado).
El mapeo del flujo de valor analiza el flujo de materiales e información a través del proceso de producción, desde las materias primas hasta el producto terminado. Es una visualización del flujo de valor, desde el inicio del proceso de producción hasta el cliente.
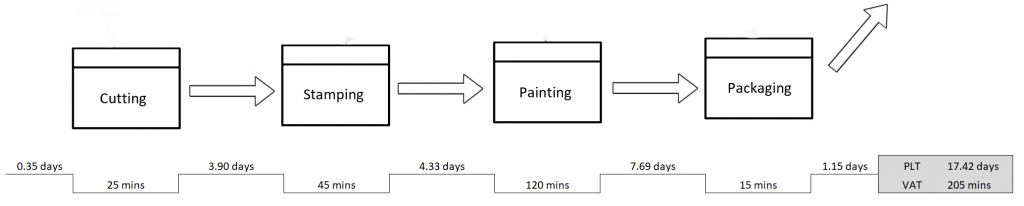
Un mapa completo de la corriente de valor incluiría muchas más piezas de información.
Los procesos no están todos dentro de la planta interna. Las técnicas de Lean Manufacturing miran todo el flujo de valor que normalmente incluye proveedores y contratistas, así como las operaciones internas.
Lean Manufacturing: Flujos
En una planta tradicional, la fabricación toma la forma de un sistema de lotes y colas. Por ejemplo, en una planta de producción de bicicletas, habría una estación para el corte de tubos, otra para la soldadura de marcos y otra para la pintura. Cada estación realiza su trabajo por lotes, es decir, se necesita un cierto número de un tipo de bicicleta, seguido de un cambio (incluido el tiempo de inactividad) al siguiente tipo o variación.
Cuanto más grandes sean los lotes, mejor, porque el objetivo es reducir al mínimo el tiempo de inactividad de la maquinaria y las personas costosas.
En cambio, una instalación de fabricación que siga la filosofía Lean se busca minimizar el tiempo de espera del inventario en lugar del tiempo de inactividad de la maquinaria. El tiempo de espera del inventario se considera un desperdicio (muda) que debe reducirse o eliminarse. Dado que el producto en sí representa el valor, dejarlo en espera en la línea de producción es un desperdicio y reduce las ganancias más que la maquinaria ociosa.
Por lo tanto, el objetivo es producir continuamente de una estación de producción a la siguiente sin que se produzca ninguna parada de inventario entre estaciones.
El producto no se detiene entre las estaciones de producción.
Cada estación dentro de la línea de producción debe tener el mismo tiempo de procesamiento, llamado takt time. Algunas estaciones necesitarán dividirse en 2, 3 o más estaciones para lograr el mismo takt time.
Para aumentar la producción, se debería crear una línea de producción idéntica y paralela.
Los resultados son:
- No es necesario pagar por todas las materias primas de inmediato
- No necesitas espacio para almacenar todo el inventario
- Puedes entregar el producto terminado al cliente más rápido
- Si el cliente quiere cambiar algo, puede hacerlo sin necesidad de una extensa revisión.
El tiempo desde la materia prima hasta el producto terminado se reduce a menudo en un 90% o más frente a la fabricación tradicional. Como resultado, es fácil aceptar los pedidos de un cliente y darle un producto terminado en su mano en horas o días en lugar de meses, lo que le permite proporcionar retroalimentación. Entonces, la retroalimentación puede ser rápidamente incorporada a la producción a través de rápidos cambios de equipo.
Procesos pull
La fabricación tradicional funciona en gran medida con un sistema de «empuje» (push). A la fábrica le gustaría vender un cierto tipo de producto, por lo que los vendedores tienen que ponerse a trabajar vendiéndolo.
La fábrica necesita producir un número significativo de productos terminados «extra» para asegurar que puedan cumplir con los pedidos urgentes inmediatamente, y muchos de ellos terminan siendo desperdiciados. Los diversos tipos y modelos se estiman en los mayores tamaños de lote posibles para que los cambios se reduzcan al mínimo.
En cambio, el lean manufacturing funciona al contrario, en un sistema «pull» (tirar). Es decir, la línea de ensamblaje no se pone en marcha hasta que un cliente pide el producto, se fabrica bajo encargo.
Además, la velocidad de la línea de montaje se controla meticulosamente para producir la cantidad justa de producto de acuerdo con la demanda.
Por ejemplo, si se prevé que la demanda será de 50 bicicletas por semana, la línea de montaje se crea para crear exactamente esa cantidad. Recuerde, esperar a la siguiente estación de ensamblaje es muda (no aporta valor), y esperar a que los productos terminados se vendan también es muda. Ambos son un desperdicio.
La velocidad de la línea de ensamblaje se llama takt time, y se mide en unidades de tiempo (minutos, horas, días) por estación de producción. El tiempo takt está continuamente alineado con la demanda del producto.
El sistema de arrastre se suele gestionar mediante un sistema llamado kanban. Cuando se recibe una orden, se crea una tarjeta kanban para el producto terminado. La tarjeta contiene un elemento de seguimiento para cada paso del proceso de fabricación y se mueve con el producto hasta que se completa. Sin tarjeta kanban, no hay producción.
Mejora continua
Como hemos contado, la fabricación ‘esbelta’ o Lean Manufacturing busca establecer un proceso de ensamblaje en el que las materias primas se convierten en el producto final sin necesidad de esperar.
Se mueven constantemente a través del proceso, y la cantidad mínima de piezas se almacenan. El cliente ordena un producto, la línea de ensamblaje es rearmada, y el primer producto está listo rápidamente.
Por supuesto, la mayoría de los productos necesitan ser enviados en lotes (enviar un lápiz a la vez sería antieconómico). Debido a esto, y a las variaciones naturales en la eficiencia de la producción que provocan una variación en la cadencia, es necesario mantener inventarios mínimos de piezas en varias etapas del proceso. De ahí que el siguiente paso sea la mejora continua, llamada kaizen.
Kaizen busca optimizar continuamente la línea de ensamblaje a través de la incesante eliminación de muda (desperdicio).
El arquitecto original del Sistema de Producción de Toyota, Taiichi Ohno, no se limitó a hablar de la reducción de los residuos, sino que especificó la eliminación total de los residuos del proceso de fabricación. Deshacerse de todos los muda debe ser despiadado.
Cuando se descubre un muda, debe ser eliminado inmediatamente, por el personal de la planta de producción si es posible, sin reuniones de planificación ni deliberaciones. El paciente está enfermo y la situación es una emergencia.
Con este fin, hay 7 tipos de muda (residuos) en la fabricación ajustada:
- La sobreproducción: Es la producción de bienes terminados que no se venden, o que deben ser almacenados por largos períodos de tiempo.
- La espera: Es el producto que espera la siguiente estación de ensamblaje, los trabajadores que esperan que la estación anterior esté completa, o que esperan debido a un fallo de la maquinaria.
- El transporte: Es el movimiento de piezas alrededor de la planta.
- El sobreprocesamiento: Es el procesamiento de un producto más allá de lo que el cliente quiere.
- El movimiento es el movimiento de personas, como los operarios que buscan herramientas, equipos o piezas.
- Inventario: Es el almacenamiento de materias primas que no se están produciendo en productos terminados. Esto ha acuñado el término fabricación justo a tiempo (Just in time).
- La fabricación de piezas defectuosas: Es la producción de productos que son desechados. Toda la línea de ensamblaje se ha desperdiciado en la producción de productos de desecho.
El Lean Manufactuing añade un muda más:
- Las habilidades no utilizadas: Son los conocimientos y habilidades que el personal de la planta tiene y que no se utilizan para mejorar el producto o reducir el muda.
El concepto de mejora continua (kaizen) busca inspeccionar continuamente el proceso de producción en busca de indicios de estos ocho muda y eliminarlos del sistema.